Yes, the U.S. can develop new battery tech
Form Energy and Natron Energy show that the U.S. can build competitive new battery technology companies. However, private-public partnerships are needed to fund inventors high-risk venture ideas.
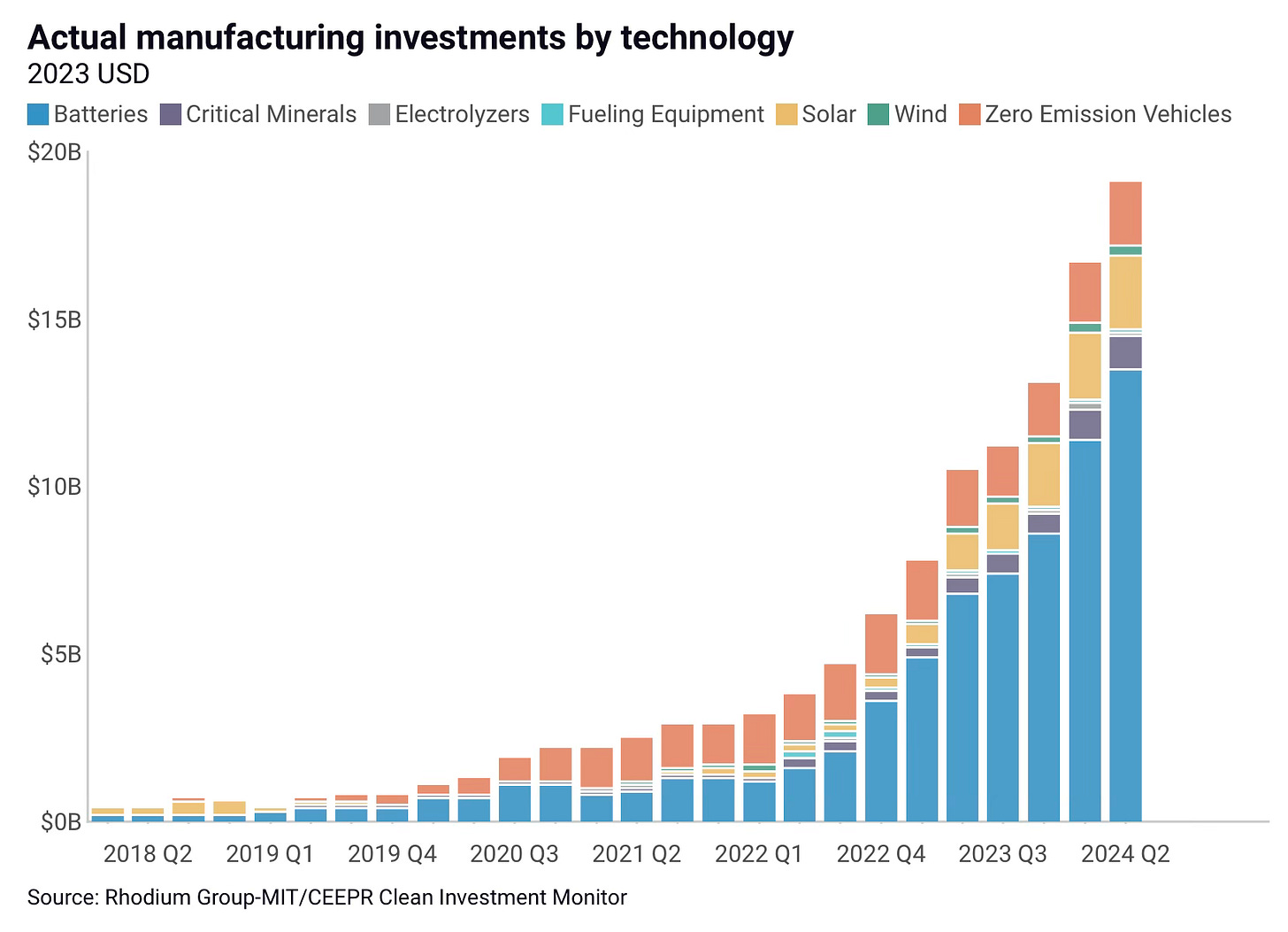
We have a new moonshot goal: electrifying America with clean energy technologies to end fossil fuel emissions and mitigate climate change risks.
How can intermittent solar and wind power help achieve this ambitious goal? One answer is to deploy utility-scale batteries to store excess solar and wind energy for later use, such as at night.
Today’s growth in utility-scale battery installations comes from short-duration lithium-ion and lower-cost lithium iron phosphate (LFP) batteries, which discharge their power in a few hours.1
The technology for utility-scale lithium batteries is an offshoot of the massive investments in electric vehicle (EV) battery development and manufacturing. The U.S., under the Inflation Reduction Act, is spurring the investment of a domestic battery supply chain. For example, in the first half of 2024, U.S. battery manufacturing investments, much of it to serve the auto industry, jumped to $24.9 billion, up from $11.7 billion in the first half of 2023, more than doubling in a year (see graph above).
Despite these efforts, the U.S. lags behind China in battery manufacturing and development. According to the National Blueprint for Lithium Batteries 2021-2013,
China is the largest global EV market and dominates the supply chain for the manufacture of lithium‑ion batteries, including the processing of minerals and raw materials. China relies on massive incentives to support domestic EV manufacturing, retail-level subsidies to create demand for domestic products, and a battery certification program to limit market access for foreign products.
Can U.S. startup companies compete with China to sell products based on new battery technology ideas developed in the laboratory?
Yes! Two companies, Form Energy and Natron Energy, are bringing new low-cost, long-duration batteries to market. These batteries solve a market need to power utilities and equipment for days, not hours, using excess solar and wind power. Even better, these new technologies do not rely on lithium or expensive lithium-ion battery chemistries.
Form Energy turns rusting iron into long-duration batteries for utilities.
To find a technology solution for a low-cost, long-duration battery, Dr. Yet-Ming Chiang, Kyocera Professor in the Department of Materials Science and Engineering at MIT, and Mateo Jaramillo, Vice President of Products and Programs for Tesla’s stationary energy storage program, “joined forces to co-found Form Energy in Somerville, Massachusetts.” [Source: MIT Energy Initiative]
Form Energy’s iron-air batteries use readily available, domestically-produced iron, a low-cost material, to create batteries that discharge saved electricity for up to four days, not just four hours.
After proving the technology, raising venture capital, signing up initial electric utility customers, and raising capital and economic development incentives, Form Energy built a new factory at the closed Weirton Steel factory site in West Virginia. Construction of the $760 million facility was just completed, and the plant is undergoing staffing and setup. By 2028, staffing is projected to be 750 people.
To encourage local economic development at the vacant steel plant, the State of West Virginia provided a $290 million financial incentive package for hiring and training local workers and providing competitive salaries. [Source: WESA, Pittsburgh’s NPR Radio]
200 interview slots were filled within 36 hours of posting jobs online, [CEO Mateo] Jaramillo said. It helps that the minimum average salary being offered is $63,000 — which is about $10,000 more than what men in the region make on average and double what women make on average.
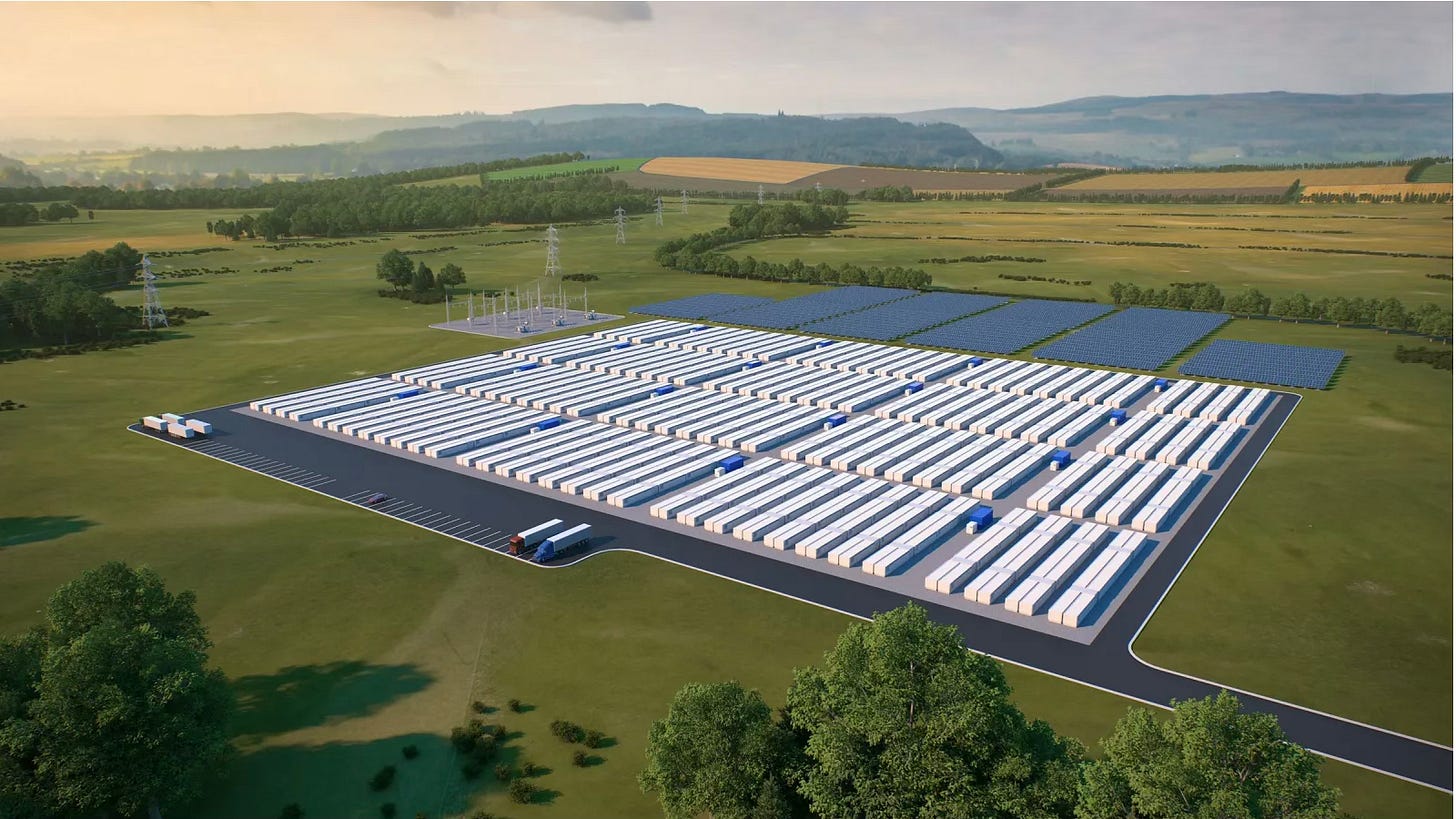
Although Form Energy has yet to start manufacturing batteries, the news and press releases highlight initial successes, including:
Groundbreaking at Great River Energy in Cambridge, Minnesota. Great River Energy is an electric cooperative serving two-thirds of Minnesota’s geography and part of Wisconsin. The utility used Form Energy’s proprietary software, Formware, to evaluate long-duration energy storage and analyze how to transition to renewable energy projects for its customers. The groundbreaking announcement on August 15, 2024, increased the project size to a 1.5 MW system with a 100-hour duration (1500 MWh).
The world’s largest battery project to be built in Maine. The New England States won a $389 million award under the 2021 Bipartisan Infrastructure Law to upgrade the region’s power grid. Under the award, Form Energy will receive $147 million to enable the grid to store future offshore wind energy. Form Energy’s battery installation will be built at the former paper mill in Lincoln, ME.
The battery system will store 85 MW of energy and discharge power over four days. According to the region’s grid operator, ISO-New England, approximately 85 MW of electricity could serve between 64,000 and 85,000 homes. (Source: Portland Press Herald)Utilities in California, Georgia, Minnesota, and Colorado to get batteries. The California Energy Commission awarded Form Energy $30 million to build a 5 MW, long-duration (4 days) battery system at the Pacific Gas & Electric Company’s Mendocino, CA electric substation. The battery system is expected to begin operation at the end of 2025 to move excess solar-generated electricity from the daytime to nighttime. Combining solar power and long-duration batteries will test California’s ability to transition to 100% clean electricity.
Georgia Power signed a definitive agreement with Form Energy to purchase a 15 MW battery storage system. The two firms will collaborate to analyze long-duration storage to meet the utility’s power deliveries as climate change increases weather uncertainty and variability. The companies will use Form Energy’s Formware software to complete the analysis.
Xcel Energy will buy two 10 MW battery systems, one each in Becker, Minnesota, and Pueblo, Colorado, to be located on former coal-fired generation plants. The utility seeks to store low-cost and abundant wind-generated electricity to displace higher natural gas costs.
Natron makes “salt” batteries for utilities and data centers.
In my Substack research brief “Beyond lithium-ion batteries, the next big thing,” I discussed Natron Energy’s sodium-ion (salt) batteries made with Prussian Blue (a common pigment) electrodes.
Natron started as a science project.
“Colin Wessells founded Natron Energy as a Stanford Ph.D. student in 2012. His vision to build a company to deliver ultra-safe, high-power batteries started in a garage in Palo Alto. After countless hours of development with an ever-growing team of scientists and engineers, Natron expanded, creating a state-of-the-art pilot production line for sodium-ion batteries in Santa Clara, California.” [Source: Natron Energy]
Sodium batteries offer advantages over lithium-ion batteries, including lower cost and the absence of expensive imported minerals such as cobalt and nickel. Additionally, compared to lithium-ion batteries, sodium-ion batteries offer fast charging (5-15 minutes compared to 2-8 hours), are nonflammable, so they are not a fire hazard, have four times the power density, and have a long life capable of 50,000 charging cycles compared to 3,500 cycles.
Natron serves industrial and utility markets for such applications as backup power for data centers, fast-charging airline ground service equipment, and backing up EV fast chargers when the utility grid is overloaded.
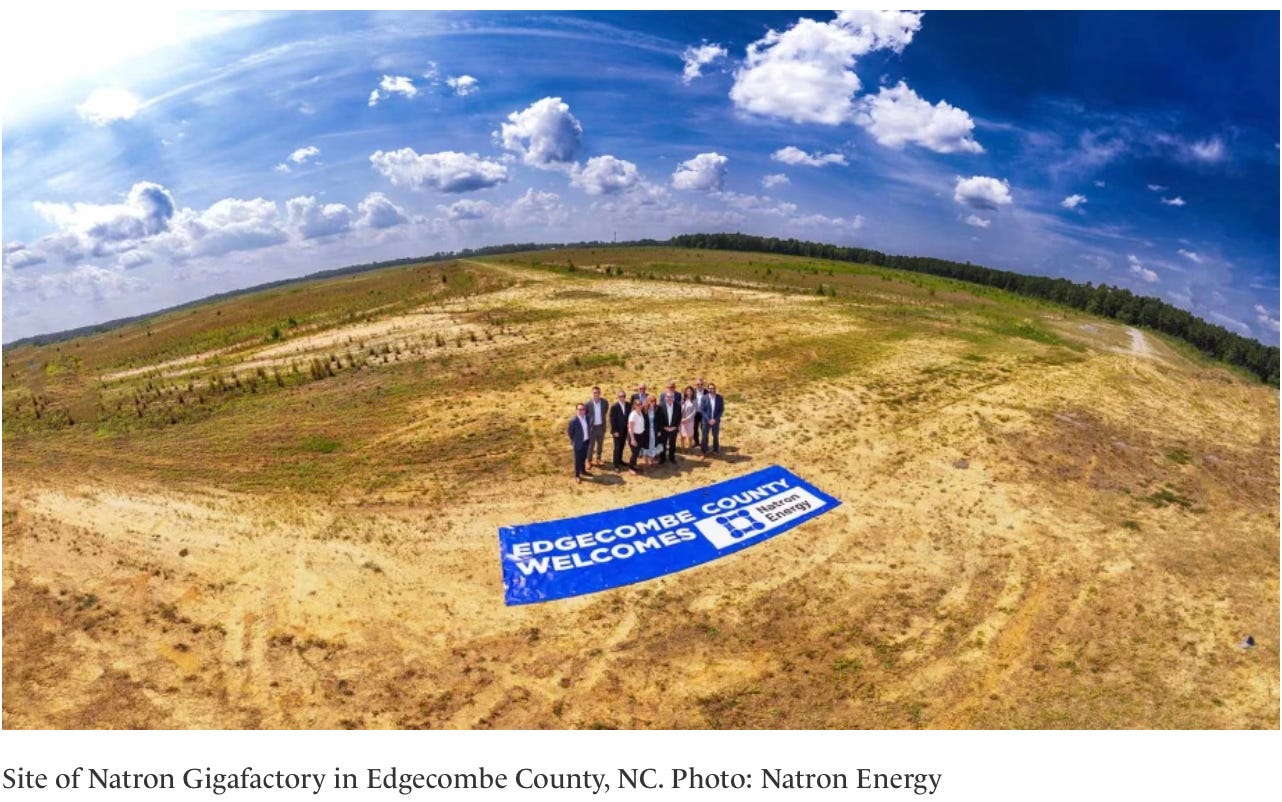
After years of development, Natron is building manufacturing plants and supporting local economic growth and jobs.
A $1.4 billion factory in Edgecombe County, North Carolina, was announced. The new facility will be constructed outside Raleigh at the Kingsboro Business Park. The site was originally planned for a Chinese tire company (Triangle Tyre) that pulled out due to tariffs. North Carolina will provide up to $50 million from the Job Development Investment Grant if the firm hires about 1062 employees at a minimum average wage of $64,071 [Source: Axios Raleigh]. Local incentives will also provide up to $130 million. Now, Natron must raise the funds to construct the plant.
The first sodium-ion battery manufacturing plant started in April 2024. Natron invested $40 million to convert an existing $300 million lithium-ion factory in Holland, MI, to sodium-ion. The Advanced Research Projects Agency-Energy (ARPA-E), an early-stage investment organization funded by the Department of Energy, provided $19.8 million. The plant will help Natron build initial products for new customers with its expected 100-person workforce.
United Airlines invested in Natron’s Holland, MI, manufacturing facility to plan to use the batteries for ground transportation electric vehicles, future airport operations, and potentially electric air taxis.
Unlike building a software business, developing, financing, and growing hardware companies requires time and money (venture capital, federal government research and development funds, state economic development funds, and private capital) to go from the inventor’s garage or university laboratory to commercial success. Tesla, one of the modern great success stories, became successful through government grants and incentive programs to fund its development and initial factories.
It is a myth that the free market will spawn and grow high-risk startup companies. Yes, there are examples in software businesses, but hardware companies, such as cleantech firms, require a basket of funds over many years to bring promising ideas to market. Building factories, supply chains, and a book of customer orders is expensive.
Tesla is a major manufacturer of U.S.-made, utility-scale LFP batteries with its new “Megafactory” in Lathrop, CA.